We provide end-to-end solution for managing Supplier Quality Management. The solution includes Qualification, Approval and Ongoing assessments. Our Audit module integrates with Supplier Quality Management to provide complete package for Supplier Quality Management.
The following are key benefits of our Supplier Quality Management Solution.
- Create and maintain approved supplier list
- Create assessment records for the suppliers
- Plan and Schedule ongoing assessments for the supplier on as needed and with automated option.
- Plan and create supplier audits on as needed and with automated option
- Generate reports and metrics for monitoring the effectiveness of the Supplier Quality Management process.
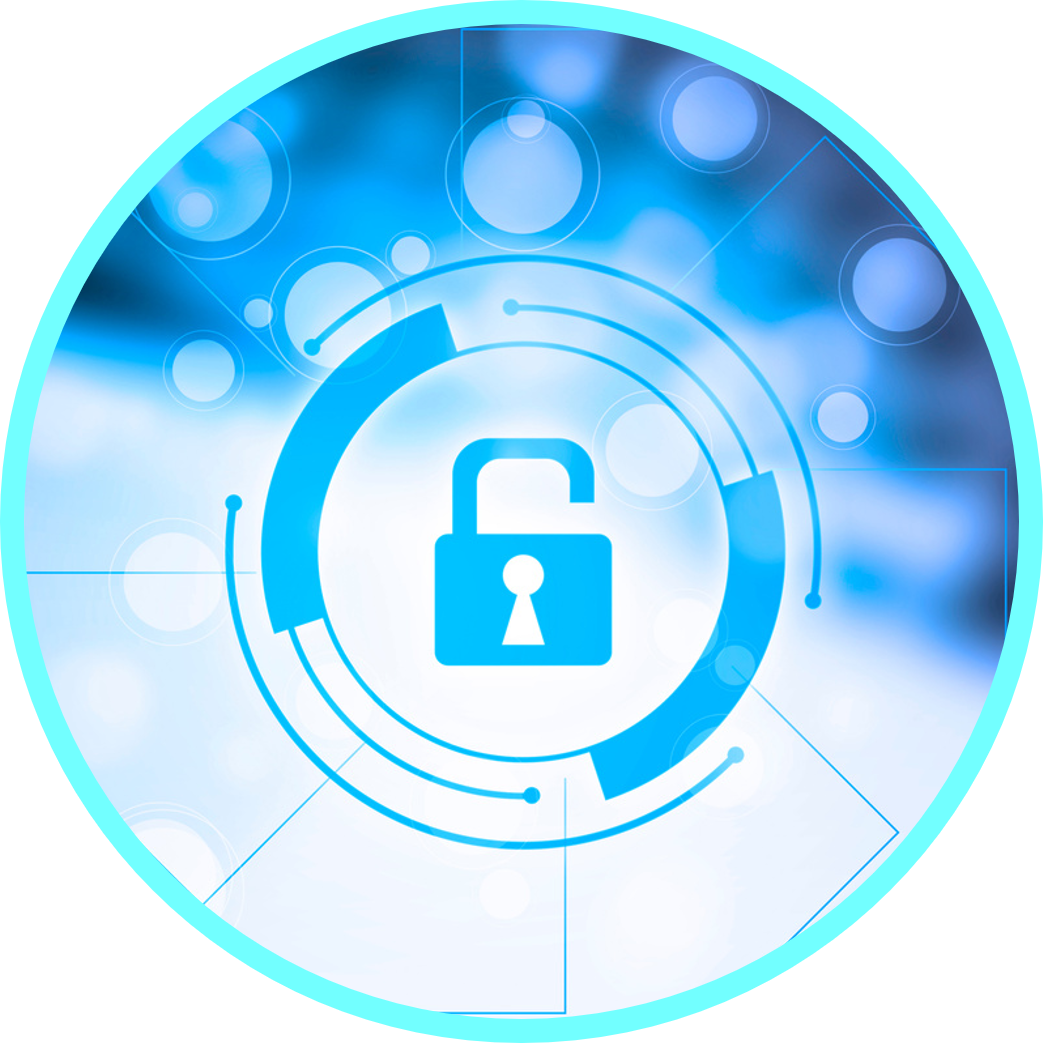
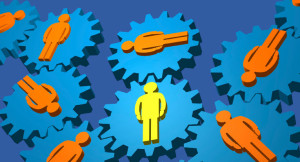
Highlights of our Supplier Quality Management Solution
Here are some of the critical questions that we have addressed with our supplier management module.
- What processes are used for evaluation of the suppliers?
- Are you using boilerplate surveys for compliance purpose only?
- Are you using onsite audits? Have the supplier audits been effective? Are you working in partnership with the suppliers to improve the quality of your products and services?
- How do you define the roles, responsibilities, specification and expectations?
- How do you monitor the ongoing performance of the suppliers? Do you do this quarterly, semiannually or annually?
- How do you select, qualify and approve the supplier for the critical products and services?
- What process is used for managing the schedule and the performance?
- What type of performance metrics you are using? Is it taking too long to generate the reports? How do you manage the overall process?
The price should not be the only criteria for selection of suppliers. The cost of nonperformance could be significant. The objective should be to minimize the total cost. We should focus on many key variables that include Quality, delivery, innovation capabilities, customer service, and organizational capability that provide best value and lowest total cost.
More about our Supplier Quality Management System
In the 21st century the organizations have more upstream and downstream linkages. There are many benefits of engaging supplier linkages. It helps the organizations to Inner-2focus on the activities that matter most from the business point.
The benefits include -leverage the economy of scale and expertise from the supplier, reduce capital expenditure, reduce time to market, increase flexibility and so on.
The quality of products and services may be directly impacted if the supplier linkages are not managed properly. There has been many examples of product recall and failure due failure from the supplier side. The recent high profile recalls of Honda,GM, Toyota and many other cars due to airbag issues from the supplier – Takata. The risk of supplier linkage increases significantly if the sourcing product is in the form of near finish component or the finished product itself.