Effective Supplier Quality Management – How to do this?
How to establish an effective supplier quality management system? Why is it important? If you are going for ISO standards or trying to comply with FDA requirements, this may have been a challenging area for you. You may have created documented procedures, forms and templates. You may be using some software solutions to manage the processes. We wanted to give you a sample proedure that may help you establish an effective supplier quality management program.
This procedure describes the process for evaluation, selection, monitoring of the performance and reevaluation of external providers (suppliers), which provide processes or products and services to your company. The evaluation and reevaluation of the suppliers is required as part of the ISO9001, ISO13485 Standard and Internal business processes. This procedure describes a risk based approach for managing the supplier quality performance with respect to ISO 13485:2016. The procedure uses reference to QSI (Qualcy Systems Inc) as the company. You can use your company name, to create your own procedure.
This procedure covers the external providers that provide products and services that may have direct or indirect impact on the quality of products and services provided by QSI to their customers. The evaluation and monitoring of the suppliers will depend upon the criticality of the products and services provided. Please refer to the section 6.0 for the definition of criticality of material and services.
FDA 21 CFR Part 820.50 Requirement:
Sec. 820.50 Purchasing controls. |
Each manufacturer shall establish and maintain procedures to ensure that all purchased or otherwise received product and services conform to specified requirements. (a) Evaluation of suppliers, contractors, and consultants. Each manufacturer shall establish and maintain the requirements, including quality requirements, that must be met by suppliers, contractors, and consultants. Each manufacturer shall: (1) Evaluate and select potential suppliers, contractors, and consultants on the basis of their ability to meet specified requirements, including quality requirements. The evaluation shall be documented. (2) Define the type and extent of control to be exercised over the product, services, suppliers, contractors, and consultants, based on the evaluation results. (3) Establish and maintain records of acceptable suppliers, contractors, and consultants. (b) Purchasing data. Each manufacturer shall establish and maintain data that clearly describe or reference the specified requirements, including quality requirements, for purchased or otherwise received product and services. Purchasing documents shall include, where possible, an agreement that the suppliers, contractors, and consultants agree to notify the manufacturer of changes in the product or service so that manufacturers may determine whether the changes may affect the quality of a finished device. Purchasing data shall be approved in accordance with 820.40. |
Who Should be Responsible for Supplier Quality Management?
The Quality Manager or the designee shall be responsible for
-> Evaluating the criticality of material and services.
-> Creating plan for evaluation, selection, monitoring of the performance and reevaluation of the suppliers
-> Provide resources and train the employee to execute the process.
Evaluation and Selection of New Suppliers for Supplier Quality Management
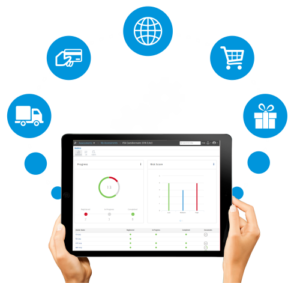
Supplier Quality Management
The supplier quality management begins with evaluation and selection for correct suppliers.
Following details will be used for evaluating the capability of new suppliers to provide material and services as per the criticality requirements.
Evaluation Requirement | Criticality3 | Criticality2 | Critiality1 |
Supplier Self Assessment* | Yes | Noc | No |
First lot inspection result | Yes | Yes | No |
*The supplier self assessment may be waived, if the supplier is registered with 3rd party (e.g. ISO or FDA).
* If the supplier is not responsive for providing the self assessment, the material from the supplier will be subject to 100% incoming inspection. The status of the supplier will be monitored.
Based on the impact to final product quality, safety and performance of the finished product, if the material or service is classified as criticality 3, then following sections shall be followed
-> Create a raw material specification or service contract document
-> Contact the supplier and send a copy of the RF0092 Supplier Self Assessment form. Request for a copy of the certification of the Quality System from 3rd party if available.
-> When the completed the form is received, review the completed form and evaluate the performance using the following formula and the table.
The percentage of Yes response = (No. of Yes response) x 100/ (Total number of questions)
% of Yes Response | Evaluation Status |
Greater than or equals to 75% | Approved |
Between 50% and 75% | Conditional |
Below 50% | Rejected |
If the supplier is classified as Conditional, the material or service from the supplier can be procured and used in production subject to following conditional requirement. After 1 year (must be before beginning of 3rd year) or after receiving 5 lots which ever happens earlier, the performance of the incoming lots and the performance of the intermediate and finished good material where the incoming lots were used shall be evaluated. If the performance has been greater than or equals to 75%, the supplier will be considered Approved. If the performance has been below 75%, the supplier will be classified as Rejected. If there is no alternate supplier available, the General Manager/Quality Manager can make the decision to continue procuring material with 100% inspection of the lots.
Monitoring Performance of Existing Suppliers
Following details will be used for ongoing monitoring of the ability and performance of the suppliers.
Monitoring Requirement | Criticality 3 | Criticality 2 | Criticality 1 |
Supplier Self Assessment* (once in every 3 years) | Yes | No | No |
Review of Inspection Results once a year | Yes | Yes | No |
*The supplier self assessment may be waived, if the supplier is registered with 3rd party (e.g. ISO or FDA).
* If the supplier is not responsive for providing the self assessment, the material from the supplier will be subject to 100% incoming inspection. The status of the supplier will be monitored as per section 9.2
For the monitoring and re-evaluation of criticality 3 suppliers, following sections shall be followed:
-> The supplier self assessment needs to be completed and reviewed once in every 3 years. The need for supplier self assessment can be waived, if the supplier is registered with 3rd party (e.g. ISO or FDA).
-> The review of the supplier self assessment shall be conducted following the above section.
-> The results of incoming inspections shall be reviewed yearly for the suppliers which have provided more than 5 lots. The yearly review may be combined with management review.
-> If the result of inspections is greater than 75%, the supplier will be considered to be approved.
-> If the performance has been below 75%, the supplier will be classified as Rejected. If there is no alternate supplier available, the General Manager/Quality Manager can make the decision to continue procuring material with 100% inspection of the lots.
For the monitoring and re-evaluation of criticality 2 suppliers, following sections shall be followed
-> The results of incoming inspections shall be reviewed yearly for the suppliers which have provided more than 5 lots. The yearly review may be combined with management review.
-> If the result of inspections is greater than 75%, the supplier will be considered to be approved.
-> If the performance has been below 75%, the supplier will be classified as Rejected. If there is no alternate supplier available, the General Manager/Quality Manager can make the decision to continue procuring material with 100% inspection of the lots.
For criticality 1 suppliers, the payment information will be kept as records of service and material received from the suppliers. Since these are lowest risk suppliers, there will not be any qualification or monitoring done for criticality 1 suppliers. If any quality issues of the in-process products or released products are linked to any of the criticality 1 suppliers, then the criticality of the supplier is to be reevaluated and proper ranking shall be assigned.
-> For the suppliers which have provided less than 5 lots in a year, the performance will be monitored as needed basis.
-> The existing suppliers will be grand fathered in as approved suppliers and be classified into the criticality depending upon the type of material supplied.
-> Handling of Nonconforming material/service from the suppliers
If the material or service is from a criticality 3 supplier, then the non-conformance will be documented using RF0009 (Out of Specification report Form) following the SOP0007 Out of Specification Policy and Procedure. When there is a trend or systemic issue is observed, then CAPA risk assessment shall be conducted. Based on the risk assessment result, supplier CAPA will be opened. The supplier CAPA will be documented using RF0094 Corrective and Preventative Action Form.
You can contact us to set up a demo to see the Qualcy Supplier Quality Management Software. Also you can get a word copy of this document.