If you are running a calibration management operation with paper based or Excel spreadsheets, it may be taking lot of your valuable time scheduling, tracking and recording data for calibration and preventative maintenance activities.It may be challenging to use the paper based specification templates to record the calibration data.Then doing the manual calculation to generate the calibration certificate can take lot of time and prone to error. The manual systems can lead to compliance issues, sometimes people forget to complete the records, or simply misplace the records.
ISO & FDA REQUIREMENT FOR CALIBRATION
MANAGEMENT
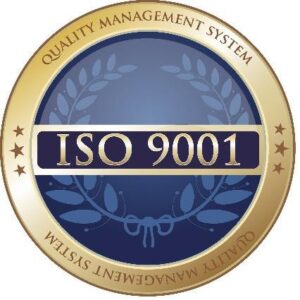
As per ISO9001:2015, section 7.1.5.1
(1)The organization will determine and provide resources necessary ensure reliable and valid results when monitoring and measuring is used to release products and
(2)The resources shall be suitable and maintained for continued successful release of the products (fitness for the purpose).
(3)The organization shall retain appropriate documented information for Calibration and Preventative Maintenance Records (as evidence of fitness for purpose) of the measurement
As per ISO9001:2015, section 7.1.5.2
(1)The organization will determine which measuring and monitoring devices that are required for providing assurance in the validity of the measurement
(2)The measurement equipment will be calibrated using standards which are traceable to NIST or international standards. When no such standards exist, the basis used for calibration will be kept as documented
(3)The measurement equipment will be identified and their status will be
(4)The measurement equipment will be protected from damage or alterations that may impact the calibration status of the
(5)When the measurement equipment are found to be out of tolerance (unfit for its intended use) the organization will determine if previous measurement results have been impacted. Based on the investigation, the organization will take appropriate actions as needed.
As per Sec. 820.70 Production and process controls.
(2) Maintenance schedule: Each manufacturer shall establish and maintain schedules for the adjustment, cleaning, and other maintenance of equipment to ensure that manufacturing specifications are met. Maintenance activities, including the date and individual(s) performing the maintenance activities, shall be documented.
As per Sec. 820.72 Inspection, measuring, and test equipment.
PART 820 — QUALITY SYSTEM REGULATION
(1) Control of inspection, measuring, and test
equipment: Each manufacturer shall ensure that all inspection, measuring, and test equipment, including mechanical, automated, or electronic inspection and test equipment, is suitable for its intended purposes and is capable of producing valid results. Each manufacturer shall establish and maintain procedures to ensure that equipment is routinely calibrated, inspected, checked, and maintained. The procedures shall include provisions for handling, preservation, and storage of equipment, so that its accuracy and fitness for use are maintained. These activities shall be documented.
(2) Calibration: Calibration procedures shall include specific directions and limits for accuracy and precision. When accuracy and precision limits are not met, there shall be provisions for remedial action to reestablish the limits and to evaluate whether there was any adverse effect on the device’s quality. These activities shall be documented.
(3) Calibration standards: Calibration standards used for inspection, measuring, and test equipment shall be traceable to national or international standards. If national or international standards are not practical or available, the manufacturer shall use an independent reproducible standard. If no applicable standard exists, the manufacturer shall establish and maintain an in- house standard.
(4) Calibration records: The equipment identification, calibration dates, the individual performing each calibration, and the next calibration date shall be documented. These records shall be displayed on or near each piece of equipment or shall be readily available to the personnel using such equipment and to the individuals responsible for calibrating the equipment.
CHALLENGES WITH MANUAL PAPER BASED SYSTEMS
Manual paper based systems are inefficient and ineffective for obvious reasons.
(1) When manual paper based systems are used, it is time consuming to create, store the records and retrieve the records.
(2) You need additional space, manpower and money to manage the manual paper records.
(3) It is almost impossible to run metrics on the paper based records
(4) Always there is chance of missing the records or misplacing the records.
(5) Higher chance of audit findings and compliance failure.
CHALLENGES WITH MANUAL EXCEL FILE SYSTEMS
Manual file keeping with Excel files and folder has its own share of issues.
(1) It is hard to control the access and changes when multiple people have access to same excel file.
(2) It is confusing to track the revision and version of the Excel files.
(3) You have to follow the nomenclatures of the files.
(4) You have to communicate the changes in the file structure with the stake holders.
(5) The location of the Excel file can be easily changed. It is hard to create any reminders in the Excel file.
Not only the manual paper based systems and Excel file folders are inefficient, these systems also create significant compliance issues and costly product recalls.
WEB BASED SOFTWARE APPLICATIONS FOR CALIBRATION MANAGEMENT
The web based software applications hosted on reputed platforms have validated the hardware and facilities.
Amazon EC2 provides platforms with documentations supporting the reliable operation of web based software applications.
Qualcy App application from Qualcy Systems is a simple web based software application hosted on the Amazon EC2 cloud.
It provides centralized data management for calibration operations.
All your data and records for the gauges, instruments and equipment are available at one single location which can be accessed by the users at anytime, anywhere on any device.
You can enter the calibration data in the field or shop floor. No need to carry the paper documents.
With the automated workflow option, you can route the calibration record for approval with click of a button. The approvers get instantly notified to review and approve.
HIGH LEVEL ORGANIZATION OF QUALCY APP APPLICATION
Qualcy App application is an integrated system that is fully compliant with the regulatory requirements and international standards including ISO and FDA requirements. This has 3 high level sub systems which work seamlessly to make calibration management simple and effective.
1.1 The first sub system is the User Management
(1) In this option you can manage Users and their Role Permissions.
(2) When a new employee joins the company, you can easily register the user and allow him the permissions necessary to get him started right away.
(3) When someone leaves the company, you can quickly deactivate their permissions in one click.
(4) To help you easily migrate your existing user data, Qualcy App has option for adding any number of users in one click using an Excel upload template.
1.2 The second sub system is the Option for Managing Master Data or Fixed Data of the gauges or equipment
(1) The examples of master data include- Description, location, owner, date of purchase.
(2) These data mostly do not change over the life cycle.
(3) You need to have master data of the equipment or gauges in the system, so that you can create records for them.
(4) To help you easily migrate the existing master data, the Qualcy App provides group addition option, you can upload any number of equipment or gauges with an Excel spreadsheet template.
1.3 The third sub system is the Option for Creating and Managing all your records for Calibration, Preventative Maintenance records and Out of tolerance records.
(1) For simple and easy navigation, the equipment master record is displayed in a tree view.
(2) Once you open the master record, you can easily access and create the calibration records and PM records with few clicks.
(3) With automated workflow option, the CAL or PM records can be automatically routed to the approvers for review.
(4) The approvers get instantly notified. No need to carry around the paper files. It saves valuable time and helps establish smooth work flow.
FEATURES AND BENEFITS OF WEB BASED APPLICATIONS IN CALIBRATION MANAGEMENT
The web base software applications provide many benefits over paper based or Excel file systems. The Qualcy App software is one of the best web based software application. This is packed with features that makes Calibration Management simple and effective.
Inbox: All your messages are stored in this page. All the messages and workflow assignments with active link inside are available here. This is a powerful option, as you can open the record directly from the message. Then you can do the transaction without spending time to search for the record.
Auto Work Flow Option: You can auto-schedule both calibration and preventative maintenance, ensuring quality management of your assets. By setting up approval requirements, records will be reviewed by the approvers automatically. The smart notifications keep everything running smoothly.
Auto schedule option: The calibration records and preventative maintenance record requirements can be set up in the auto schedule option. The system will create the blank records and send reminders to the owner to complete their task in time and complete the records. The Qualcy App application provides reminders to owners of the tasks when it is coming due.
Search Option: You can use the search menu option and find the records based on query selection. You can search for the records by status, owner, approver, date created, and many other variables. You can export the records to excel format also.
Save: You can save any of your search query and give a name. This name can be made available under the menu items. When you click on this menu item, it runs the same query. So this option provides users to build custom menu items.
Reports: You can quickly run reports and see the trends for overdue calibration, PM or OOT records. You can run reports by equipment, by owner, by location and many other variables. You can use these reports for management review.
Use of Calibration Templates: You need calibration templates to record and maintain consistency in Calibration data. Qualcy App provides option to build flexible templates for the gauges and instruments. Once created, those templates are available over the life cycle of the instrument to help you maintain consistency of data.
Printing of calibration Certificates and Labels: The calibration records and the PM records and OOT records can be printed in the .pdf format. Also the calibration label can be printed from the system. You can print the .pdf reports of the calibration certificates when needed. No need to store the paper documents.
Option for managing OOT (out of tolerance records): When the calibration results fail, you can create out of tolerance records. The details of investigation for product impact can be documented in the OOT record. You can set up the review and approval of the OOT records as per your requirement. You can easily run metrics to see the trends for history of equipment failures and take preventative actions as needed.
Audit trail option: Any changes made during the life cycle of the records is automatically logged with time stamp. You can easily access the audit trails and confirm the changes made by the users when needed. This is one of the key requirements to comply with the 21 CFR Part11.
Security and back up of Data: It is very critical that the best industry standard is followed to maintain the security and back up of the data. You do not want to take any chances. Qualcy App uses Amazon EC2 cloud servers for individual customer data management. Each customer has their dedicated servers. The customers have the options to share the application with 3rd parties ( including suppliers and customers)
You can contact us to set up a demo to see the Qualcy Calibration Management Software. Also you can get a word copy of this document.